時間:2023-11-24 17:31來源:原創(chuàng) 作者:智泰咨詢 點擊:
次
什么是快速換模?
Single Minutes Exchange of Dies.
SMED系統(tǒng):是一種能有效縮短產品切換時間的理論和方法。
什么是快速換模?
Single Minutes Exchange of Dies.
SMED系統(tǒng):是一種能有效縮短產品切換時間的理論和方法。
SMED在50年代初期起源于日本;由(新江重夫)在豐田企業(yè)發(fā)展起來;
Single的意思是小于10分鐘(Minutes);
最初使用在汽車制造廠,以達到快速的模具切換(Exchange of Dies);豐田現場人員經過長期探索,將沖壓工序沖床模具裝換調整所需時間,從1945年至1954年的3小時,縮短為1970年以后的3分鐘,現在,豐田汽車公司利用設備快速裝換調整SMED法,所有大中型設備的裝換調整作業(yè)均能在10分鐘之內完成。企業(yè)產品切換時間由4小時縮短為3分鐘。
常見換模的基本構成:
切換時間的定義:
從上一個產品生產結束到下一個合格品生產出來并達到設計速度所需的時間
換模過程中的時間損失:
SMED內外部時間定義:
內部時間:
只有當機器停下來才能進行的操 作所需要的時間
外部時間
可以在機器運行的情況下進行的 操作所需要的時間
SMED 進程:
SMED實施步驟:
第一步:
1.區(qū)分內部和外部的工作
1.1將機器運行時即能做的工作和必須停機才能做的工作分開;
1.2 浪費時間的實例(內部時間≥外部時間)
1.2.1 停機以后才將部件或工具移至機器處;
1.2.2 在裝配時才發(fā)現工具或部件的缺陷;
1.2.3 在部件安裝好后才發(fā)現部件的缺陷;
1.2.4 在裝配過程中更換和維修部件;
1.2.5 在裝配過程中尋找部件、螺釘、材料等.
1.2.準備和使用檢查表
1.2.1 列出切換工作中需要的所有東西
1.2.1.1 工具、部件、標準操作規(guī)程以及需要的人員
1.2.1.2 合適的操作條件---溫度、壓力、轉換開關設置、閥門等.
1.2.1.3 產品的規(guī)格和尺度
1.2.2 標出已經準備好的項目
1.2.3 對于每一個操作過程均使用檢查表
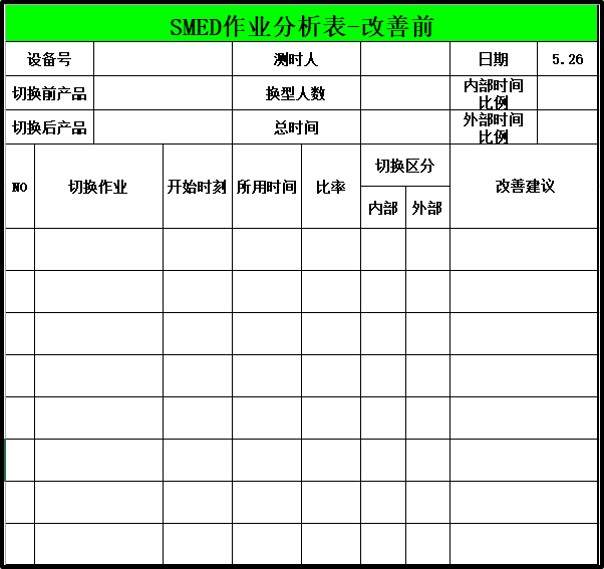
1.3.進行功能檢查
1.3.1 檢查在切換時所有要使用的配件、工具狀況是良好、功能是否齊全;
1.3.2 切換開始前(30分鐘前)就要檢查,以及時進行修理;
1.3.3 切換前要進行核對所需項目是否與要求一致。
1.4.改進部件和工具的運輸
1.4.1 所有新的部件和工具必須在停機前運到現場≥外部操作
1.4.2 所有換下的部件和工具應在切換結束后才進行清理和轉存≥外部操作
1.4.3 將部件、工具存放于工作現場,切換時只動手不動腳
1.4.4 降低運輸的時間和人力(人數)
1.4.5 使工具和部件容易找到和存放
1.4.6 機臺在停機前,準備切換的模具要及時到 位于機臺合適的位置
第二步:
2.1.將內部操作轉化為外部操作
2.1.1了解每一步內部操作的真實目的和作用;
2.1.2找尋可將內部操作轉化為外部操作的途經;
2.1.3以陌生的眼光觀察目前的切換過程,只當是第一次看到一樣.
2.2.預先準備操作條件
2.2.1 在切換開始前,準備好所需的材料、部件、工具和條件(溫度、壓力)
2.2.1.1檢查儀表
2.2.1.2將物品放在合適的位置
2.2.1.2預熱
2.2.1.3制作臨時支架
2.3.功能標準化
2.3.1確定哪些功能可進行標準化,將外部尺寸、備件、設置標準化,以便部件能很容易更換
2.3.2盡可能少地更換部件(Zero !)
2.4.使用中間夾具/模塊(部件集成化)
2.4.1 使用中間夾具或模塊
2.4.2 使用具有標準的外部尺寸和固定裝置的中間夾具或模塊
2.4.3 在機器停機之前在中間夾具/模塊上進行裝 配(外部時間)
2.4.4 在停車后將夾具/模具一次性更換(內部時間)
第三步:
3.1.優(yōu)化切換操作的各方面
3.1.1 了解切換每個操作的作用和目的并詢問:怎樣更進一步改善切換時間 ?
3.1.2 優(yōu)化內部操作
3. 1.2.1增強平行操作;
3.1.2.2多功能性夾具;
3.1.2.3調試的消除,對不可避免的進行改善;
3.1.2.4利用機械化;
3.1.3 優(yōu)化外部操作,包括貯存和運輸原材料部件及工具:
3.1.3.1不必尋找配件和工具;
3.1.3.2不會使用錯誤的配件和工具;
3.1.3.3不要進行不必要的移動。
3.2.調試的消除
3.2.1 試運行和調整占總切換時間的30%;
3.2.2 盡量消除調試,而不僅是減少;
3.2.3 目標:一次性成功;
3.2.4 在裝配過程中使用標準程序,并進行雙重檢查;
3.2.5 提高裝配技能(多一點學習)
3.2.6 提高裝配可靠性的技巧:
3.2.6.1 使用標準設置以固定數字刻度/標尺;
3.2.6.2 可視化的設置值和參照線;
3.2.6.3 最小公倍數原理;
3.2.6.4 傻瓜也能進行的裝配 (防錯法)。
3.3.改善不可避免的調試
3.3.1 量化
3.3.1.1 什么時候需要 ? (在X個小時運轉或者生產Y個產品后)
3.3.1.2 可以接受的偏差范圍 ?
3.3.1.3 需要采集樣本/數據 ?
3. 3.2 制訂調試的程序:
3.3.2.1 規(guī)范的程序圖。
3.3.3 提高調試的技能:
3. 3.3.1 現場培訓。
第四步:
4.1.經驗和教訓
4. 1.1 集中精力于工藝過程,不僅是依靠改進 設備
4.1.1.1發(fā)生切換時的時間節(jié)省程度多與操作順序有關進行切換和平行工作時將切換部件移至它們應在位置。
4.1.2 切換的改進不應只由工程部門完成
4.1.2.1 SMED是一種系統(tǒng)化的方法,易于團隊成員使用
4.1.2.2 每個人都積極參加
4.1.3 在實踐過程中,將不斷積累的經驗標準化,制定相應的標準
更多精益管理內容請查閱:
精益管理:
八大浪費:
智泰咨詢公司給企業(yè)提供專業(yè)的5S管理,6S管理,TPM管理落地輔導與培訓服務;給企業(yè)提供免費上門調研服務和5S,6S管理,TPM管理定制化落地輔導方案。
聯(lián)系電話/微信:137 5118 4775
智泰咨詢公司承諾達成以下共同約定的三大目標:
一、企業(yè)形象影響力提升:
手把手輔導打造一個規(guī)范、整潔、高效、安全的工作環(huán)境,隨時可參觀,可檢查,可介紹的生產標桿現場---提升企業(yè)新訂單接單率;
二、企業(yè)管理人才培養(yǎng):
給企業(yè)培養(yǎng)一批熟練掌握6S管理、TPM管理、精益管理、QC七工具、8D改善法等等管理工具的優(yōu)秀人才---保證企業(yè)可持續(xù)高速發(fā)展;
三、生產各項指標提升:
生產效率提升50%以上;產品質量提升度30%以上;生產經營成本下降10%以上;設備故障率下降70%以上---確保成為行業(yè)標桿和最高競爭力企業(yè)。
(責任編輯:智泰咨詢)